Automated Fulfilment: The Future of Order Processing is Here
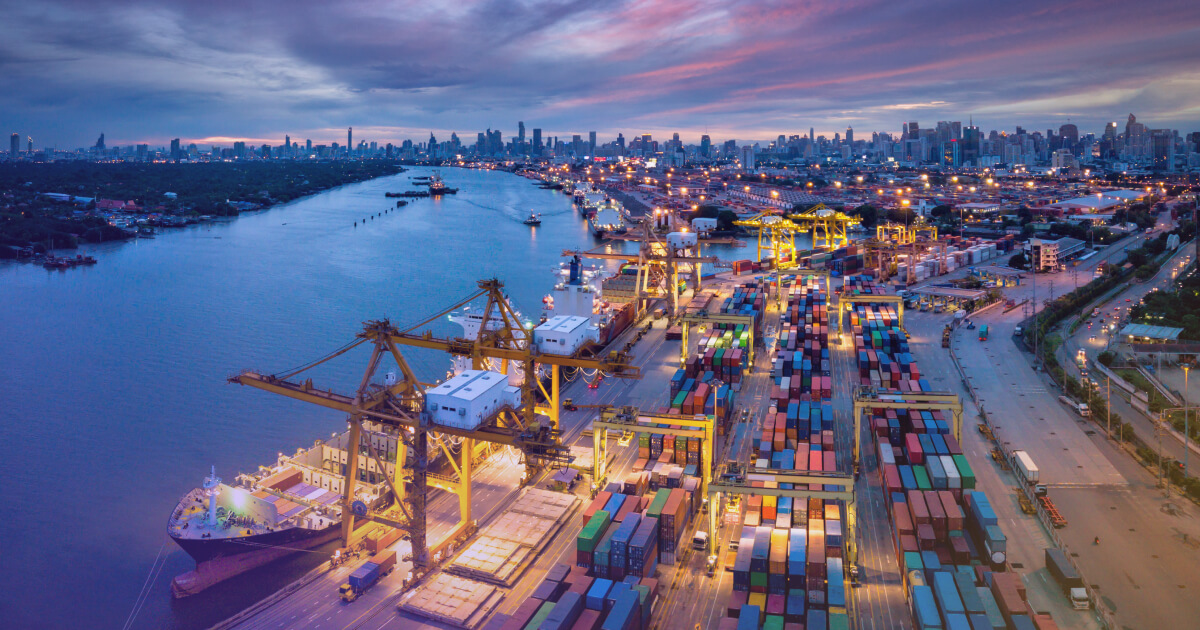
Automated fulfilment is the process by which orders are processed and shipped automatically without human intervention. This is done with the help of advanced technologies and algorithms designed to manage inventory, order processing, and shipping.
The rise of ecommerce has created a need for automated fulfilment as the number of orders processed every day continues to increase. This trend is driven by the need for timely and accurate delivery of products to customers in different parts of the world.
With the increasing demand for faster delivery and the growing number of online stores, automated fulfilment is becoming more critical than ever. This technology allows online retailers to streamline their operations, reduce the time and money spent on manual order processing and shipping, as well as improve accuracy and efficiency.
As such, automated fulfilment is increasingly becoming a vital component of the ecommerce industry, allowing retailers to meet the growing demand while remaining competitive in the rapidly evolving online marketplace.
A brief history of order processing in ecommerce
Order processing in ecommerce has a long history that began in the 1990s…
With the emergence of the internet, companies started to offer their products and services online. Initially, order processing was carried out through email and phone calls, which was time-consuming and inefficient.
However, with the development of online payment systems and software, companies began to adopt an automated approach to order processing. This led to the introduction of order management systems and shopping carts that allowed customers to choose products, make payments, and receive order confirmations in real-time.
Over the years, companies have continued to refine their order processing systems, with the introduction of new technologies such as artificial intelligence and blockchain, which have made order processing faster, more efficient and more secure than ever before through intelligent data extraction, better customer service and enhanced privacy features (such as two-factor authentication and encryption),
Today, ecommerce companies are able to process orders more quickly and accurately, enabling them to deliver products to customers anywhere in the world.
The Need for Automated Fulfilment in Ecommerce
With the rapid growth of ecommerce throughout the coronavirus pandemic, many businesses struggled to keep up with the demand for quick and efficient fulfilment of goods ordered online. Manual systems for fulfilment are not only slow and inefficient, but also prone to human errors such as mistakes in data entry, inventory management, packaging, communications and documentation - to name just a few!
This is where automated fulfilment comes in.
Automated systems use technology such as robotics, artificial intelligence and machine learning to streamline the entire fulfilment process, from receiving orders to shipping products to customers. Not only does this process save time and money, but it also greatly reduces the risk of errors and delays.
Automated fulfilment allows businesses to seamlessly manage high volumes of orders, improving the overall customer experience and increasing customer satisfaction. In today's fast-paced ecommerce world, automated fulfilment is becoming a necessity for businesses to stay competitive and meet the rising expectations of customers.
Benefits of Automated Fulfilment
With the help of automation technologies like robots, conveyor belts and software, businesses can streamline their order processing and fulfilment processes:
- Increased efficiency: Automated fulfilment systems can significantly improve operational efficiency by reducing manual labour, eliminating errors and streamlining processes. Tasks such as order processing, picking, packing and shipping can be automated, resulting in faster order fulfilment and reduced processing time.
- Cost savings: Automation can lead to cost savings in several areas. By reducing the need for manual labour, businesses can save on expenses and overheads. Automation can also minimise errors and improve inventory management, reducing costs associated with order inaccuracies, stockouts and overstocking.
- Enhanced accuracy: Automated systems offer high levels of accuracy and precision, minimising errors in order fulfilment. With advanced technologies such as barcode scanning and automated sorting, the likelihood of incorrect shipments or misplaced items is significantly reduced, resulting in improved customer satisfaction and reduced return rates.
- Scalability and flexibility: Automated fulfilment systems can easily scale up or down based on demand fluctuations. They can handle increased order volumes without significant additional manpower, allowing businesses to adapt to peak seasons or sudden surges in orders.
- Improved inventory management: Automation enables real-time tracking and monitoring of inventory levels, reducing the risk of stockouts or overstocking. Integrated inventory management systems can provide accurate inventory information, enabling businesses to optimise their stock levels, make data-driven decisions, and avoid excess inventory carrying costs.
- Faster order processing and delivery: Automated systems can expedite order processing, resulting in faster order fulfilment and delivery. With automated picking and packing processes, orders can be processed and dispatched quickly, meeting customer expectations for shorter delivery times and improving the overall customer experience.
- Data-driven insights: Automated fulfilment systems generate a wealth of data related to order processing, inventory management and customer behaviour. By analysing this data, businesses can gain valuable insights into trends, customer preferences, and operational performance.
- Improved customer experience: Automation can lead to a better customer experience through faster order processing, accurate shipments, and timely delivery. Automated systems also enable better order tracking and transparency, allowing customers to stay informed about their order status. Enhanced customer experience leads to higher customer satisfaction, repeat business and positive word-of-mouth.
- Reduced physical labour risks: Automation reduces the physical strain on employees, minimising the risk of workplace injuries and repetitive strain injuries associated with manual labour tasks. This can contribute to a safer working environment and improved employee well-being.
Challenges of Automated Fulfilment
Despite its numerous benefits, automated fulfilment also presents a unique set of challenges that needs to be addressed.
From technological complexities and integration hurdles to workforce implications and ethical considerations, businesses must navigate these obstacles effectively to fully harness the potential of automated fulfilment.
- Technological complexities: Implementing automated fulfilment systems requires sophisticated technologies such as robotics, conveyors, sorting mechanisms and advanced software. Integrating and managing these complex systems can pose challenges in terms of design, installation, maintenance, and troubleshooting.
- Integration hurdles: Integrating automated fulfilment systems with existing infrastructure, such as inventory management systems, order processing software, and customer relationship management (CRM) platforms, can be a complex task. Ensuring seamless communication and data exchange between different systems is crucial for efficient operations. This is where Codept comes in. Our one-time integration for ERP-, shop- and WMS-systems, facilitated by an experienced team of software engineers, ensures that businesses are set up for flexibility and scalability.
- Workforce implications: While automated fulfilment can improve operational efficiency, it also raises concerns about the impact on the workforce. Traditional manual tasks may be automated, leading to job displacement or a need for reskilling and redeployment of employees. Managing this transition and ensuring a smooth integration between humans and machines is a significant challenge.
- Creating complex automations: Previously, creating complex workflows has been a deterrent for merchant adoption of automated fulfilment, with fears of conditional logic, rules and configurations not working how they’re supposed to! However, with Codept, manual tasks become less challenging through native functionality and system integrations across shop-, ERP-, and WMS-systems. Our trusted partners bring additional functionality that frees up IT resources so they have more time for strategic projects.
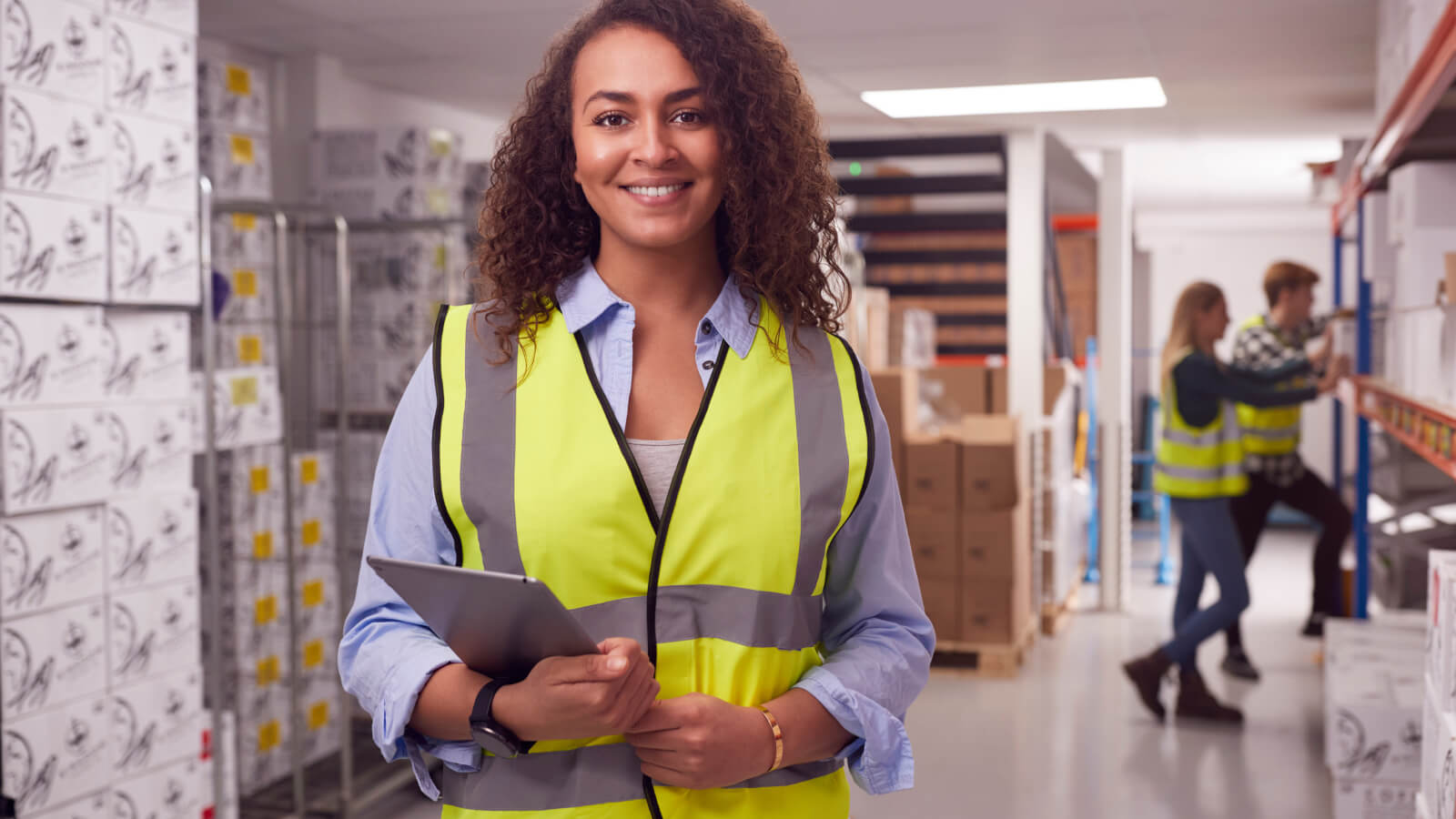
- Scalability and adaptability: As businesses grow and consumer demands evolve, automated fulfilment systems need to be scalable and adaptable. Ensuring that the systems can handle increased order volumes, new product lines, and changing fulfilment requirements requires careful planning and continuous optimisation.
- Operational complexities: Operating an automated fulfilment system involves coordinating multiple processes, such as order processing, inventory management, picking, packing, and shipping. Managing the complexities of these interconnected operations, including optimising workflows, minimising errors and maintaining quality control, can be demanding.
- Cost considerations: While automated fulfilment systems offer long-term cost savings, the initial investment can be significant. Procuring and implementing the required technologies, training staff, and maintaining the systems can involve substantial financial resources. Balancing the cost of automation with the potential benefits is a key challenge for businesses.
- Customer experience and satisfaction: While automation can enhance efficiency, it is crucial to maintain a high level of customer experience and satisfaction throughout the fulfilment process. Our solution allows businesses to find the right and most cost-effective fulfilment provider for their and their customers' needs. We enable businesses to build a logistics network that saves time and money whilst offering better visibility through a centralised solution. Ensuring accurate order fulfilment, timely delivery, effective communication and easy returns handling are critical challenges in automated fulfilment that Codept helps businesses to overcome, by providing a scalable integration platform.
- System reliability and downtime: Automated fulfilment systems heavily rely on technology, and any system failures or downtime can have severe consequences on business productivity and profitability. Ensuring system reliability, implementing effective backup and redundancy measures as well as minimising downtime are essential challenges to overcome.
- Environmental impact: While automated fulfilment can reduce operational costs and improve efficiency, its environmental impact must also be considered. Energy consumption, carbon emissions, waste management and sustainable packaging are challenges that need to be addressed to minimise the ecological footprint of automated fulfilment systems. Where environmental impact is a key aspect of a merchant’s fulfilment, Codept’s Tender Management solution identifies suitable partners that meet these green credentials.
The Components of Automated Fulfilment
Automated fulfilment comprises several interconnected components that work together to streamline the order processing and delivery operations. These components include inventory management, order management, and shipping automation:
1. Inventory Management
Efficient inventory management is crucial for automated fulfilment. It involves tracking and organising inventory levels, ensuring accurate stock counts and managing replenishment.
Automated inventory management systems utilise technologies such as barcode scanning, RFID tagging and real-time data synchronisation to provide accurate inventory information.
These systems enable businesses to monitor stock levels, anticipate demand, and automate the reordering process, ensuring optimal inventory levels and reducing the risk of stockouts or overstocking.
2. Order Management
Order management encompasses the processes involved in receiving, processing, and fulfilling customer orders.
In automated fulfilment, order management systems play a vital role in handling order data, automating order processing workflows, and ensuring efficient order fulfilment. These systems receive order information from various channels, such as ecommerce platforms or point-of-sale systems, and integrate it with inventory data. They facilitate order routing, picklist generation, and order tracking.
Automated order management systems enable businesses to streamline the order processing cycle, minimise errors, and ensure timely fulfilment.
3. Shipping Automation
Shipping automation focuses on automating the packing, labelling and shipping processes. Automated packing systems use robotics, conveyor belts, and sorting mechanisms to efficiently pack items based on order specifications.
They can handle different package sizes and shapes, optimise packaging materials and print shipping labels. Once the items are packed, automated shipping systems generate shipping labels, calculate shipping costs and integrate with shipping carriers' systems to schedule pickups and track shipments.
Shipping automation ensures accurate and timely dispatch of orders, reduces manual handling errors, and improves the overall efficiency of the fulfilment process.
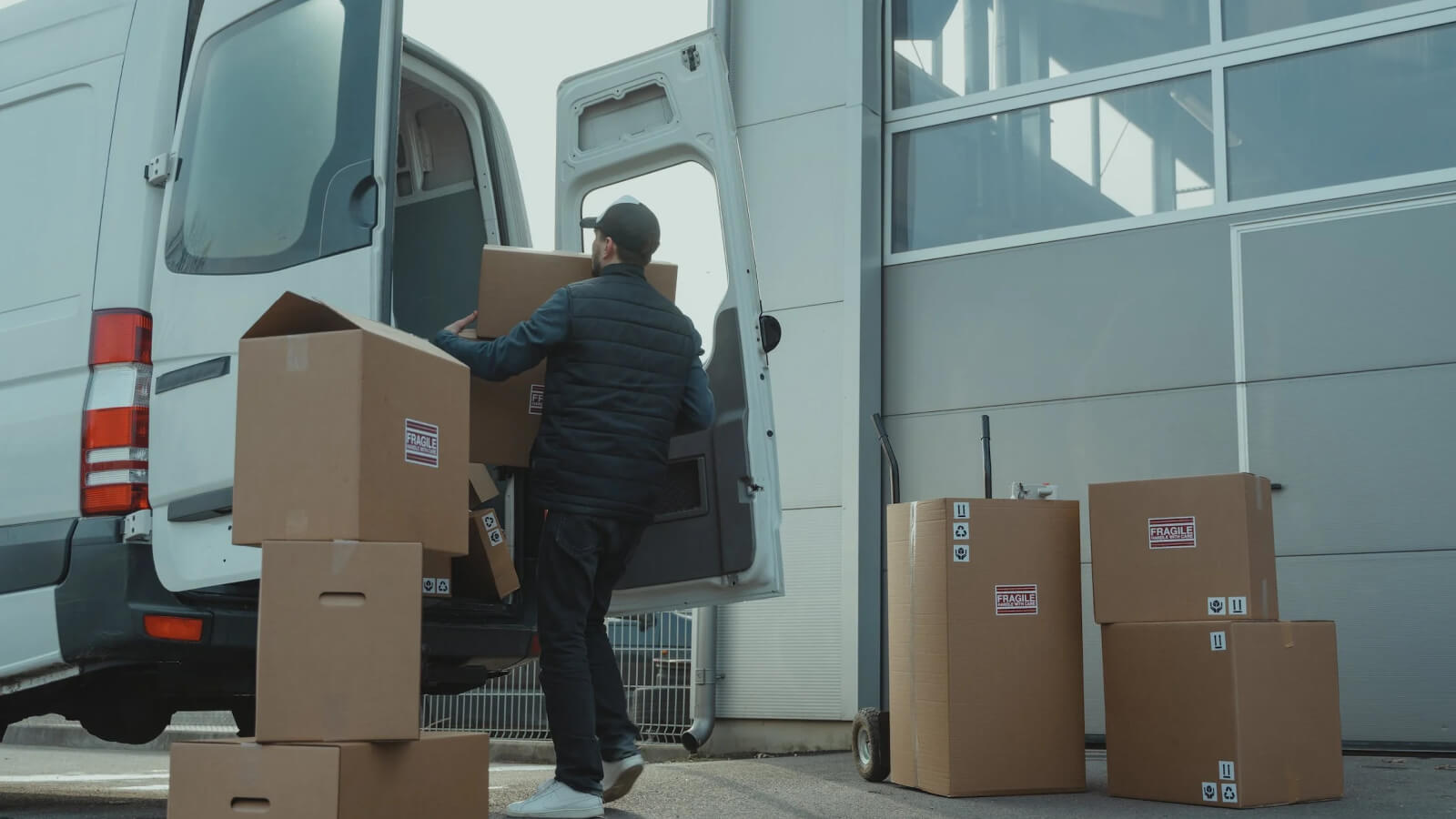
The integration and synchronisation of inventory management, order management and shipping automation are crucial to achieving a seamless automated fulfilment process.
Choosing the Right Automated Fulfilment Solution
When considering the implementation of an automated fulfilment system, selecting the right solution is critical to achieving operational efficiency and customer satisfaction. The market offers a variety of automated fulfilment solutions, each with its own set of features and capabilities.
Types of automated fulfilment solutions
- Warehouse Automation Systems: These solutions focus on automating various aspects of warehouse operations, including inventory management, order picking, packing and shipping. They typically involve the use of robotics, conveyor systems, automated guided vehicles (AGVs) and advanced warehouse management software.
- Automated Sorting Systems: These solutions are designed to streamline the sorting process in distribution centres or fulfilment centres. They utilise conveyor systems, barcode scanners and sorting mechanisms to efficiently route items to their respective destinations based on order specifications.
- Automated Packing Systems: These solutions aim to automate the packing process by using robotic arms, computer vision and smart algorithms to pack items into boxes or packages. They optimise packing density, reduce packaging material waste and improve packing accuracy.
- Integrated Order Management Systems: These solutions focus on automating the end-to-end order management process, from order entry to fulfilment. They handle tasks such as order routing, inventory synchronisation, order tracking and customer notifications. These systems often integrate with other software applications, such as ecommerce platforms and shipping carriers.
Factors to consider when choosing an automated fulfilment solution
To make an informed decision, businesses must carefully assess their specific needs and consider factors such as scalability, integration and cost:
Scalability
It is essential to assess the scalability of the automated fulfilment solution.
Consider whether the system can handle increasing order volumes and accommodate future growth. Scalability allows businesses to adapt to changing demands and prevent bottlenecks in the fulfilment process.
By unifying logistics integrations with Codept, our customers benefit from smoother connections between multiple providers.
Integration
Compatibility and integration with existing systems are crucial for a seamless automated fulfilment process. Evaluate whether the solution can be integrated with inventory management systems, order management software, ecommerce platforms and shipping carriers. Smooth data flow between different systems is essential for accurate inventory management and efficient order processing.
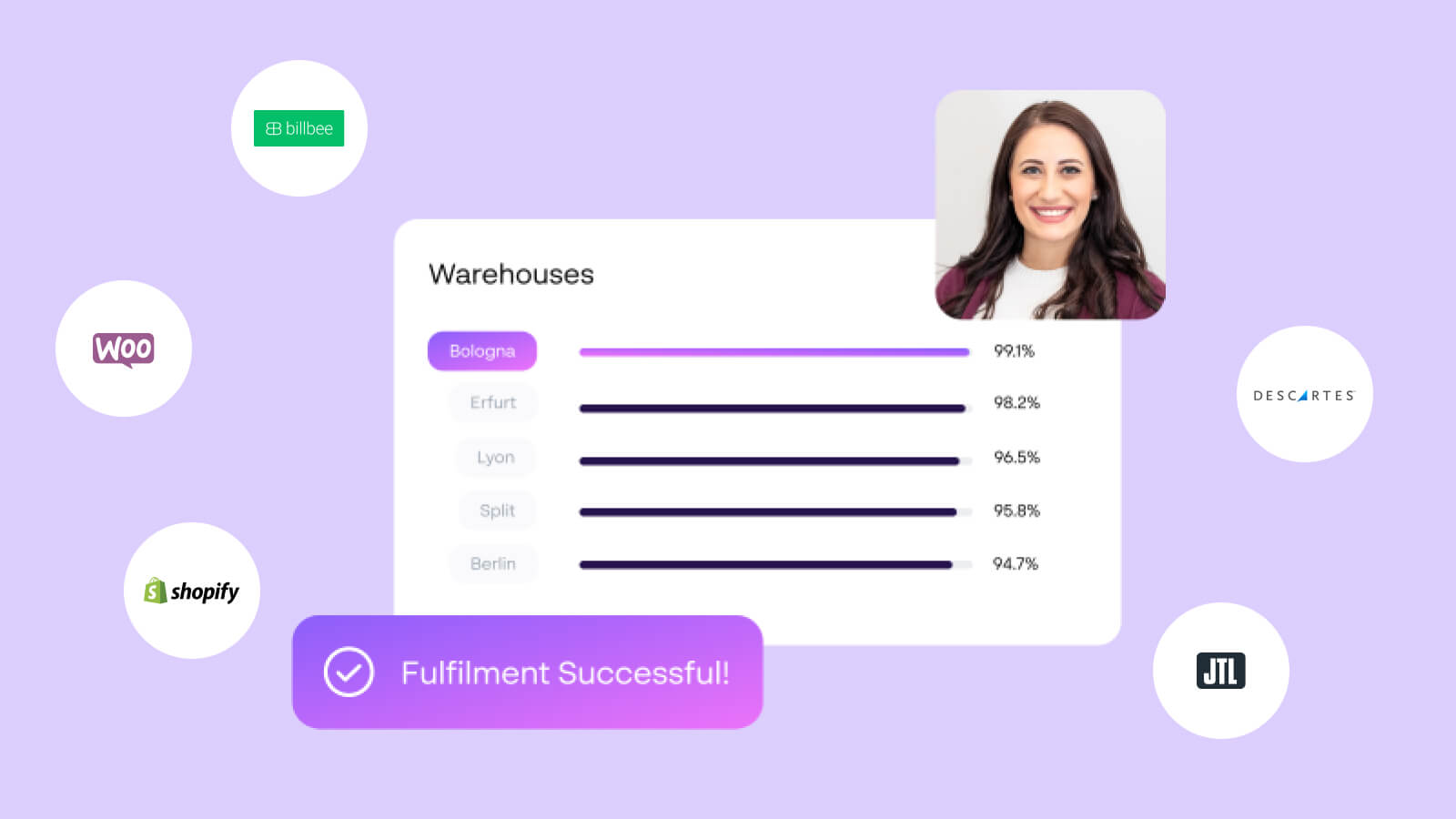
Codept’s one-time integration allows businesses to ‘plug-and-play’ additional partners and integrations as networks expand and connections between multiple ecommerce platforms and 3PLs are required.
Cost
Assessing the total cost of implementation is vital when choosing an automated fulfilment solution. Consider not only the initial investment but also ongoing maintenance costs, software licensing fees and potential training expenses.
Calculate the potential return on investment (ROI) and evaluate the long-term cost savings and operational efficiencies that the solution can provide.
Codept’s one-time connection and intuitive interface streamlines onboarding, saving time and money.
Outsourcing automated fulfilment to a third-party provider
Outsourcing automated fulfilment to a third-party provider can offer numerous benefits - let's explore these aspects in more detail…
- Expertise and Infrastructure: Third-party providers specialising in automated fulfilment have extensive expertise and infrastructure dedicated to efficient order processing and delivery. They possess the necessary technologies, equipment and skilled personnel to handle fulfilment operations effectively.
- Scalability and Flexibility: Outsourcing to a third-party provider allows businesses to leverage the provider's scalable infrastructure and adapt to fluctuating order volumes. This is particularly beneficial for merchants selling seasonal items; if less warehouse space is needed, this is easily adjustable as providers can quickly modify resources and staffing levels to meet peak demands, ensuring timely order fulfilment. Dropshipping is also an effective solution to cope with seasonal demands, since this allows ecommerce merchants to offer products in their online shop without storing or shipping items themselves. This ensures the merchant does not remain stuck with unsold goods. Using Codept’s solution enables dropshipping through fast, secure, and error-free data flow between manufacturers, wholesalers, online merchants and carriers.
- Reduced Capital Expenditure: By outsourcing automated fulfilment, businesses can avoid substantial upfront investments in equipment, software, and infrastructure. Instead, they can benefit from the provider's existing resources and pay for services based on usage or contractual agreements.
- Focus on Core Competencies: Outsourcing fulfilment allows businesses to focus on their core competencies, such as product development, marketing, and customer engagement. By offloading the complexities of fulfilment to a specialised provider, companies can allocate their resources and efforts to strategic areas of growth and differentiation.
- Faster Time-to-Market: Third-party providers with established automated fulfilment capabilities can expedite the implementation process. Businesses can quickly onboard and integrate with the provider's systems, reducing the time required to launch or scale their fulfilment operations. This accelerated time-to-market can be particularly advantageous when businesses need to rapidly respond to market demands or seasonal peaks.
- Risk Mitigation: By entrusting fulfilment operations to a third-party provider, businesses can mitigate risks associated with technology investments, system failures and operational disruptions. Providers are responsible for maintaining and upgrading their systems, ensuring high availability and managing potential risks. This allows businesses to focus on their core operations without the burden of dealing with fulfilment-related risks.
- International Expansion: For businesses looking to expand globally, outsourcing automated fulfilment to a third-party provider with an established international network can be highly advantageous. These providers often have fulfilment centres in multiple countries, enabling faster and more cost-effective international shipping, customs compliance and localised customer support. This is particularly beneficial for merchants shipping hazardous goods due to special law regulations they must comply with.
Selecting the right automated fulfilment solution requires a thorough evaluation of scalability, integration capabilities and cost considerations. Codept’s Tender Management solution helps businesses make an informed decision by identifying the most suitable partners for their assortment needs.
So, is automated fulfilment the future?
The answer lies in striking the right balance between automation and human oversight.
While automated fulfilment offers numerous benefits, it is essential to recognise the importance of human involvement in ensuring quality control and customer satisfaction.
While automation streamlines processes, humans provide the critical element of judgement, problem-solving and adaptability. Human oversight is necessary to monitor automated systems, address exceptions or errors and make decisions when unexpected situations arise.
By combining the efficiency of automation with human expertise and oversight, businesses can create a future of automated fulfilment that optimises operations, maintains quality control and delivers exceptional customer experiences.
FAQs about Automated Fulfilment
How does automated fulfilment enhance order processing efficiency?
Automated fulfilment streamlines the order processing workflow by leveraging technologies such as robotics, conveyor systems and intelligent software. These technologies enable faster and more accurate order picking, packing, and shipping, reducing human errors and optimising operational efficiency.
Will automation replace human workers in the order processing industry?
While automation plays a significant role in order processing, it is important to note that human workers still have crucial roles in overseeing and managing automated systems. Human oversight ensures quality control and exception handling.
What are the benefits of implementing automated fulfilment?
Automated fulfilment offers several benefits, including increased order accuracy, faster order processing and shipping, improved inventory management, reduced operational costs, and enhanced customer satisfaction. It allows businesses to scale their operations efficiently and handle higher order volumes with ease.
How can automated fulfilment adapt to changing customer demands?
Automated fulfilment systems can be flexible and adaptable to changing customer demands. They can handle various order types, including single-item orders, multiple-item orders and customisations.
Additionally, automated systems can be easily reprogrammed or reconfigured to accommodate new products or changes in order processing requirements.
What are the challenges of implementing automated fulfilment?
Implementing automated fulfilment can pose challenges such as the initial capital investment required for technology acquisition and implementation, the need for employee training and change management, potential disruptions during the transition period, and ensuring seamless integration with existing systems.
With proper planning and execution, these challenges can be overcome, and the long-term benefits of automated fulfilment outweigh the initial obstacles. By working with Codept, businesses can rest assured that integrations between shop-, ERP- and WMS-systems and algorithms will work frictionlessly, tested and optimised by our IT experts, making sure your system runs exactly as you need it to.
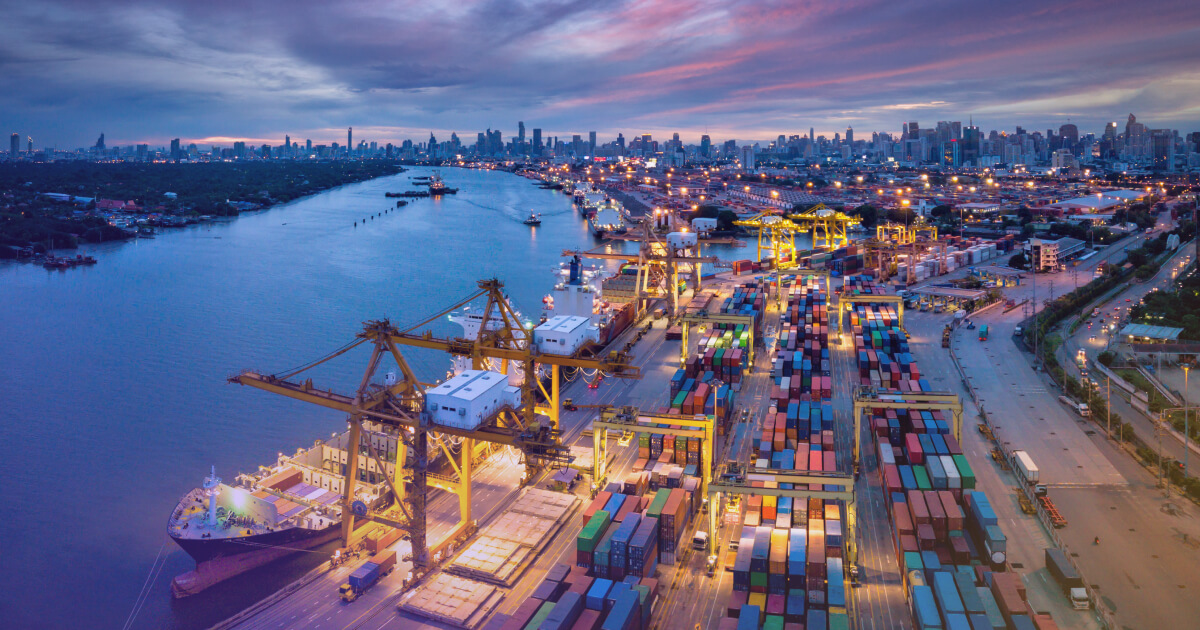
Automated fulfilment is the process by which orders are processed and shipped automatically without human intervention. This is done with the help of advanced technologies and algorithms designed to manage inventory, order processing, and shipping.
The rise of ecommerce has created a need for automated fulfilment as the number of orders processed every day continues to increase. This trend is driven by the need for timely and accurate delivery of products to customers in different parts of the world.
With the increasing demand for faster delivery and the growing number of online stores, automated fulfilment is becoming more critical than ever. This technology allows online retailers to streamline their operations, reduce the time and money spent on manual order processing and shipping, as well as improve accuracy and efficiency.
As such, automated fulfilment is increasingly becoming a vital component of the ecommerce industry, allowing retailers to meet the growing demand while remaining competitive in the rapidly evolving online marketplace.
A brief history of order processing in ecommerce
Order processing in ecommerce has a long history that began in the 1990s…
With the emergence of the internet, companies started to offer their products and services online. Initially, order processing was carried out through email and phone calls, which was time-consuming and inefficient.
However, with the development of online payment systems and software, companies began to adopt an automated approach to order processing. This led to the introduction of order management systems and shopping carts that allowed customers to choose products, make payments, and receive order confirmations in real-time.
Over the years, companies have continued to refine their order processing systems, with the introduction of new technologies such as artificial intelligence and blockchain, which have made order processing faster, more efficient and more secure than ever before through intelligent data extraction, better customer service and enhanced privacy features (such as two-factor authentication and encryption),
Today, ecommerce companies are able to process orders more quickly and accurately, enabling them to deliver products to customers anywhere in the world.
The Need for Automated Fulfilment in Ecommerce
With the rapid growth of ecommerce throughout the coronavirus pandemic, many businesses struggled to keep up with the demand for quick and efficient fulfilment of goods ordered online. Manual systems for fulfilment are not only slow and inefficient, but also prone to human errors such as mistakes in data entry, inventory management, packaging, communications and documentation - to name just a few!
This is where automated fulfilment comes in.
Automated systems use technology such as robotics, artificial intelligence and machine learning to streamline the entire fulfilment process, from receiving orders to shipping products to customers. Not only does this process save time and money, but it also greatly reduces the risk of errors and delays.
Automated fulfilment allows businesses to seamlessly manage high volumes of orders, improving the overall customer experience and increasing customer satisfaction. In today's fast-paced ecommerce world, automated fulfilment is becoming a necessity for businesses to stay competitive and meet the rising expectations of customers.
Benefits of Automated Fulfilment
With the help of automation technologies like robots, conveyor belts and software, businesses can streamline their order processing and fulfilment processes:
- Increased efficiency: Automated fulfilment systems can significantly improve operational efficiency by reducing manual labour, eliminating errors and streamlining processes. Tasks such as order processing, picking, packing and shipping can be automated, resulting in faster order fulfilment and reduced processing time.
- Cost savings: Automation can lead to cost savings in several areas. By reducing the need for manual labour, businesses can save on expenses and overheads. Automation can also minimise errors and improve inventory management, reducing costs associated with order inaccuracies, stockouts and overstocking.
- Enhanced accuracy: Automated systems offer high levels of accuracy and precision, minimising errors in order fulfilment. With advanced technologies such as barcode scanning and automated sorting, the likelihood of incorrect shipments or misplaced items is significantly reduced, resulting in improved customer satisfaction and reduced return rates.
- Scalability and flexibility: Automated fulfilment systems can easily scale up or down based on demand fluctuations. They can handle increased order volumes without significant additional manpower, allowing businesses to adapt to peak seasons or sudden surges in orders.
- Improved inventory management: Automation enables real-time tracking and monitoring of inventory levels, reducing the risk of stockouts or overstocking. Integrated inventory management systems can provide accurate inventory information, enabling businesses to optimise their stock levels, make data-driven decisions, and avoid excess inventory carrying costs.
- Faster order processing and delivery: Automated systems can expedite order processing, resulting in faster order fulfilment and delivery. With automated picking and packing processes, orders can be processed and dispatched quickly, meeting customer expectations for shorter delivery times and improving the overall customer experience.
- Data-driven insights: Automated fulfilment systems generate a wealth of data related to order processing, inventory management and customer behaviour. By analysing this data, businesses can gain valuable insights into trends, customer preferences, and operational performance.
- Improved customer experience: Automation can lead to a better customer experience through faster order processing, accurate shipments, and timely delivery. Automated systems also enable better order tracking and transparency, allowing customers to stay informed about their order status. Enhanced customer experience leads to higher customer satisfaction, repeat business and positive word-of-mouth.
- Reduced physical labour risks: Automation reduces the physical strain on employees, minimising the risk of workplace injuries and repetitive strain injuries associated with manual labour tasks. This can contribute to a safer working environment and improved employee well-being.
Challenges of Automated Fulfilment
Despite its numerous benefits, automated fulfilment also presents a unique set of challenges that needs to be addressed.
From technological complexities and integration hurdles to workforce implications and ethical considerations, businesses must navigate these obstacles effectively to fully harness the potential of automated fulfilment.
- Technological complexities: Implementing automated fulfilment systems requires sophisticated technologies such as robotics, conveyors, sorting mechanisms and advanced software. Integrating and managing these complex systems can pose challenges in terms of design, installation, maintenance, and troubleshooting.
- Integration hurdles: Integrating automated fulfilment systems with existing infrastructure, such as inventory management systems, order processing software, and customer relationship management (CRM) platforms, can be a complex task. Ensuring seamless communication and data exchange between different systems is crucial for efficient operations. This is where Codept comes in. Our one-time integration for ERP-, shop- and WMS-systems, facilitated by an experienced team of software engineers, ensures that businesses are set up for flexibility and scalability.
- Workforce implications: While automated fulfilment can improve operational efficiency, it also raises concerns about the impact on the workforce. Traditional manual tasks may be automated, leading to job displacement or a need for reskilling and redeployment of employees. Managing this transition and ensuring a smooth integration between humans and machines is a significant challenge.
- Creating complex automations: Previously, creating complex workflows has been a deterrent for merchant adoption of automated fulfilment, with fears of conditional logic, rules and configurations not working how they’re supposed to! However, with Codept, manual tasks become less challenging through native functionality and system integrations across shop-, ERP-, and WMS-systems. Our trusted partners bring additional functionality that frees up IT resources so they have more time for strategic projects.
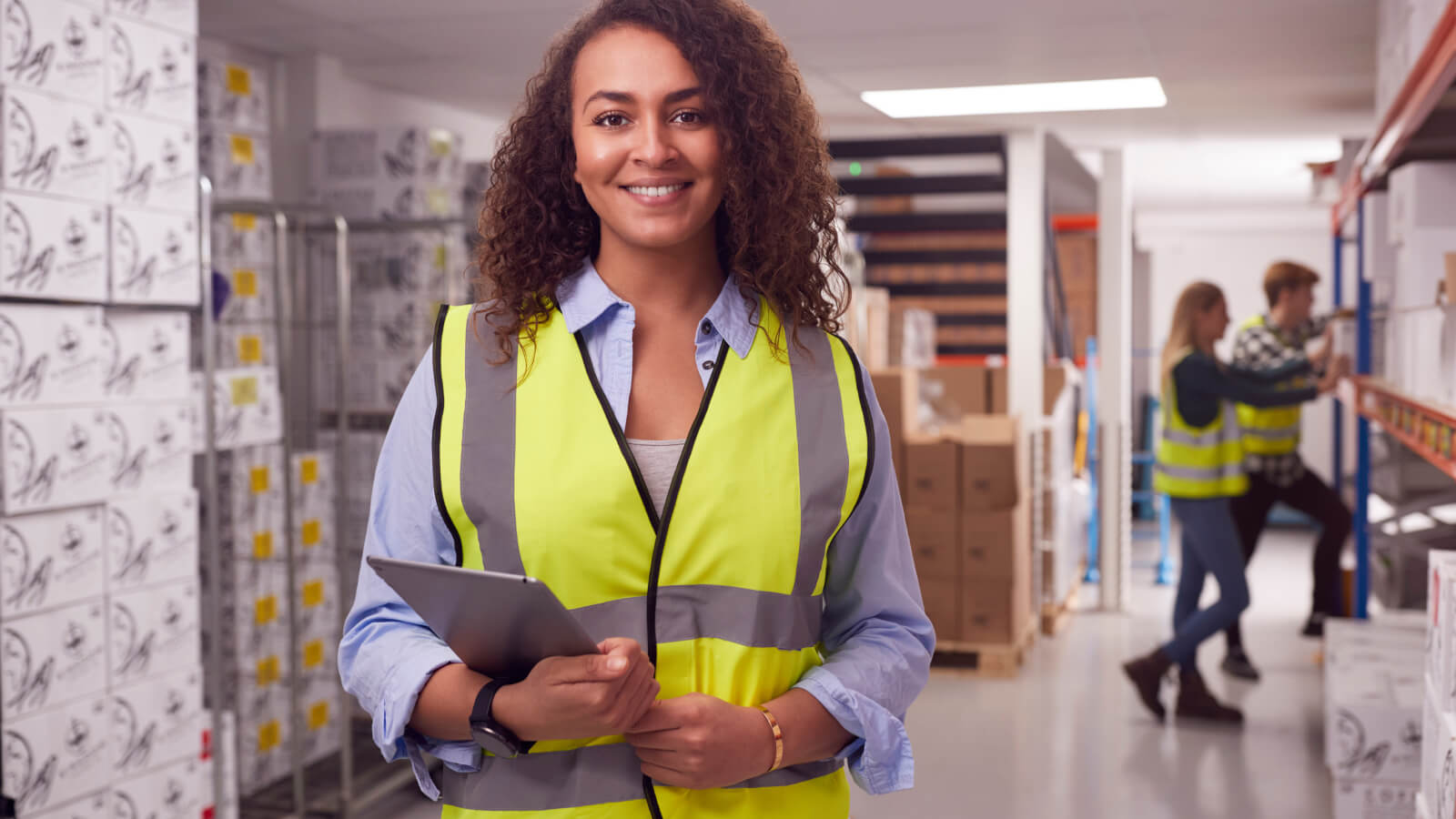
- Scalability and adaptability: As businesses grow and consumer demands evolve, automated fulfilment systems need to be scalable and adaptable. Ensuring that the systems can handle increased order volumes, new product lines, and changing fulfilment requirements requires careful planning and continuous optimisation.
- Operational complexities: Operating an automated fulfilment system involves coordinating multiple processes, such as order processing, inventory management, picking, packing, and shipping. Managing the complexities of these interconnected operations, including optimising workflows, minimising errors and maintaining quality control, can be demanding.
- Cost considerations: While automated fulfilment systems offer long-term cost savings, the initial investment can be significant. Procuring and implementing the required technologies, training staff, and maintaining the systems can involve substantial financial resources. Balancing the cost of automation with the potential benefits is a key challenge for businesses.
- Customer experience and satisfaction: While automation can enhance efficiency, it is crucial to maintain a high level of customer experience and satisfaction throughout the fulfilment process. Our solution allows businesses to find the right and most cost-effective fulfilment provider for their and their customers' needs. We enable businesses to build a logistics network that saves time and money whilst offering better visibility through a centralised solution. Ensuring accurate order fulfilment, timely delivery, effective communication and easy returns handling are critical challenges in automated fulfilment that Codept helps businesses to overcome, by providing a scalable integration platform.
- System reliability and downtime: Automated fulfilment systems heavily rely on technology, and any system failures or downtime can have severe consequences on business productivity and profitability. Ensuring system reliability, implementing effective backup and redundancy measures as well as minimising downtime are essential challenges to overcome.
- Environmental impact: While automated fulfilment can reduce operational costs and improve efficiency, its environmental impact must also be considered. Energy consumption, carbon emissions, waste management and sustainable packaging are challenges that need to be addressed to minimise the ecological footprint of automated fulfilment systems. Where environmental impact is a key aspect of a merchant’s fulfilment, Codept’s Tender Management solution identifies suitable partners that meet these green credentials.
The Components of Automated Fulfilment
Automated fulfilment comprises several interconnected components that work together to streamline the order processing and delivery operations. These components include inventory management, order management, and shipping automation:
1. Inventory Management
Efficient inventory management is crucial for automated fulfilment. It involves tracking and organising inventory levels, ensuring accurate stock counts and managing replenishment.
Automated inventory management systems utilise technologies such as barcode scanning, RFID tagging and real-time data synchronisation to provide accurate inventory information.
These systems enable businesses to monitor stock levels, anticipate demand, and automate the reordering process, ensuring optimal inventory levels and reducing the risk of stockouts or overstocking.
2. Order Management
Order management encompasses the processes involved in receiving, processing, and fulfilling customer orders.
In automated fulfilment, order management systems play a vital role in handling order data, automating order processing workflows, and ensuring efficient order fulfilment. These systems receive order information from various channels, such as ecommerce platforms or point-of-sale systems, and integrate it with inventory data. They facilitate order routing, picklist generation, and order tracking.
Automated order management systems enable businesses to streamline the order processing cycle, minimise errors, and ensure timely fulfilment.
3. Shipping Automation
Shipping automation focuses on automating the packing, labelling and shipping processes. Automated packing systems use robotics, conveyor belts, and sorting mechanisms to efficiently pack items based on order specifications.
They can handle different package sizes and shapes, optimise packaging materials and print shipping labels. Once the items are packed, automated shipping systems generate shipping labels, calculate shipping costs and integrate with shipping carriers' systems to schedule pickups and track shipments.
Shipping automation ensures accurate and timely dispatch of orders, reduces manual handling errors, and improves the overall efficiency of the fulfilment process.
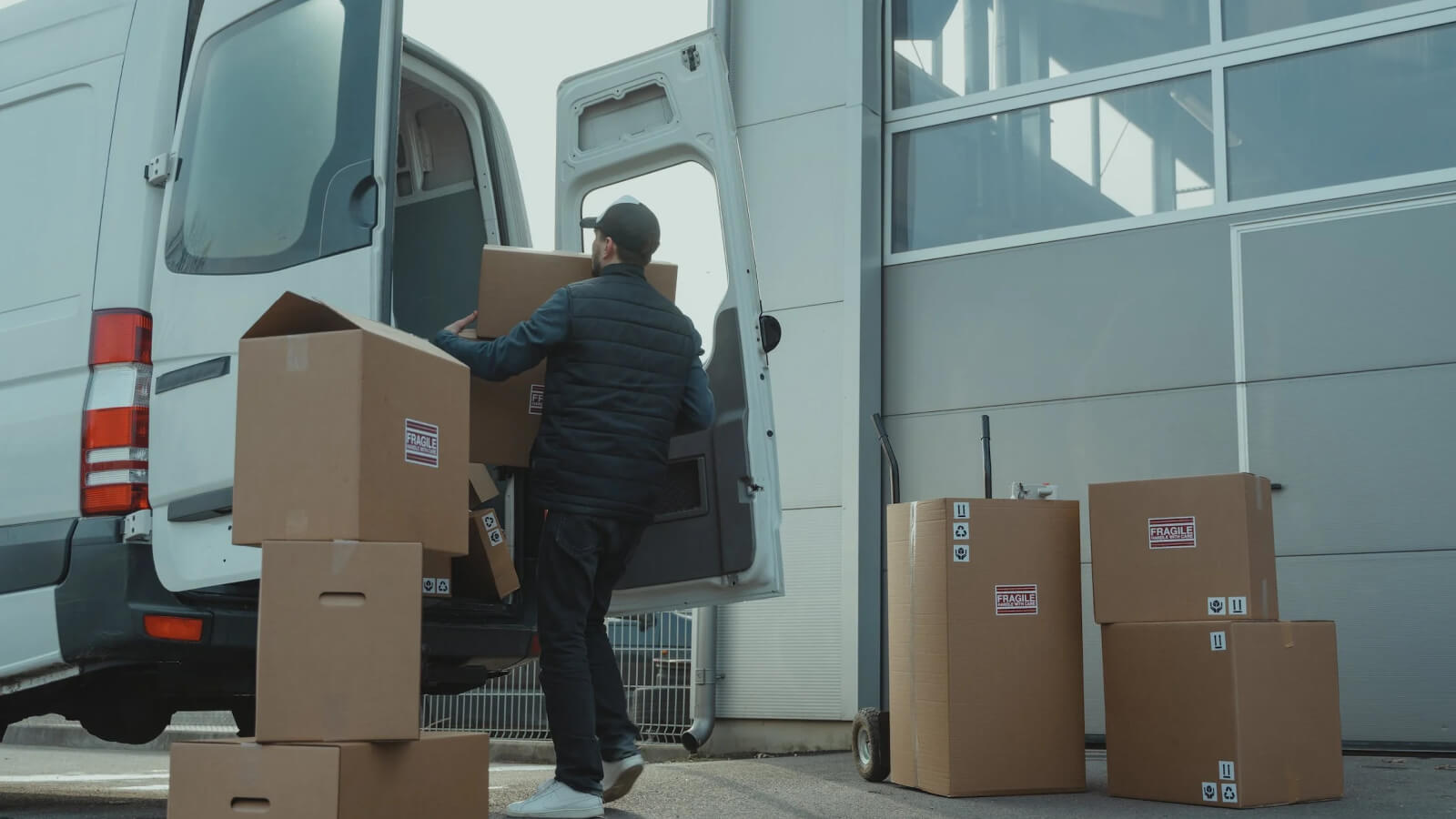
The integration and synchronisation of inventory management, order management and shipping automation are crucial to achieving a seamless automated fulfilment process.
Choosing the Right Automated Fulfilment Solution
When considering the implementation of an automated fulfilment system, selecting the right solution is critical to achieving operational efficiency and customer satisfaction. The market offers a variety of automated fulfilment solutions, each with its own set of features and capabilities.
Types of automated fulfilment solutions
- Warehouse Automation Systems: These solutions focus on automating various aspects of warehouse operations, including inventory management, order picking, packing and shipping. They typically involve the use of robotics, conveyor systems, automated guided vehicles (AGVs) and advanced warehouse management software.
- Automated Sorting Systems: These solutions are designed to streamline the sorting process in distribution centres or fulfilment centres. They utilise conveyor systems, barcode scanners and sorting mechanisms to efficiently route items to their respective destinations based on order specifications.
- Automated Packing Systems: These solutions aim to automate the packing process by using robotic arms, computer vision and smart algorithms to pack items into boxes or packages. They optimise packing density, reduce packaging material waste and improve packing accuracy.
- Integrated Order Management Systems: These solutions focus on automating the end-to-end order management process, from order entry to fulfilment. They handle tasks such as order routing, inventory synchronisation, order tracking and customer notifications. These systems often integrate with other software applications, such as ecommerce platforms and shipping carriers.
Factors to consider when choosing an automated fulfilment solution
To make an informed decision, businesses must carefully assess their specific needs and consider factors such as scalability, integration and cost:
Scalability
It is essential to assess the scalability of the automated fulfilment solution.
Consider whether the system can handle increasing order volumes and accommodate future growth. Scalability allows businesses to adapt to changing demands and prevent bottlenecks in the fulfilment process.
By unifying logistics integrations with Codept, our customers benefit from smoother connections between multiple providers.
Integration
Compatibility and integration with existing systems are crucial for a seamless automated fulfilment process. Evaluate whether the solution can be integrated with inventory management systems, order management software, ecommerce platforms and shipping carriers. Smooth data flow between different systems is essential for accurate inventory management and efficient order processing.
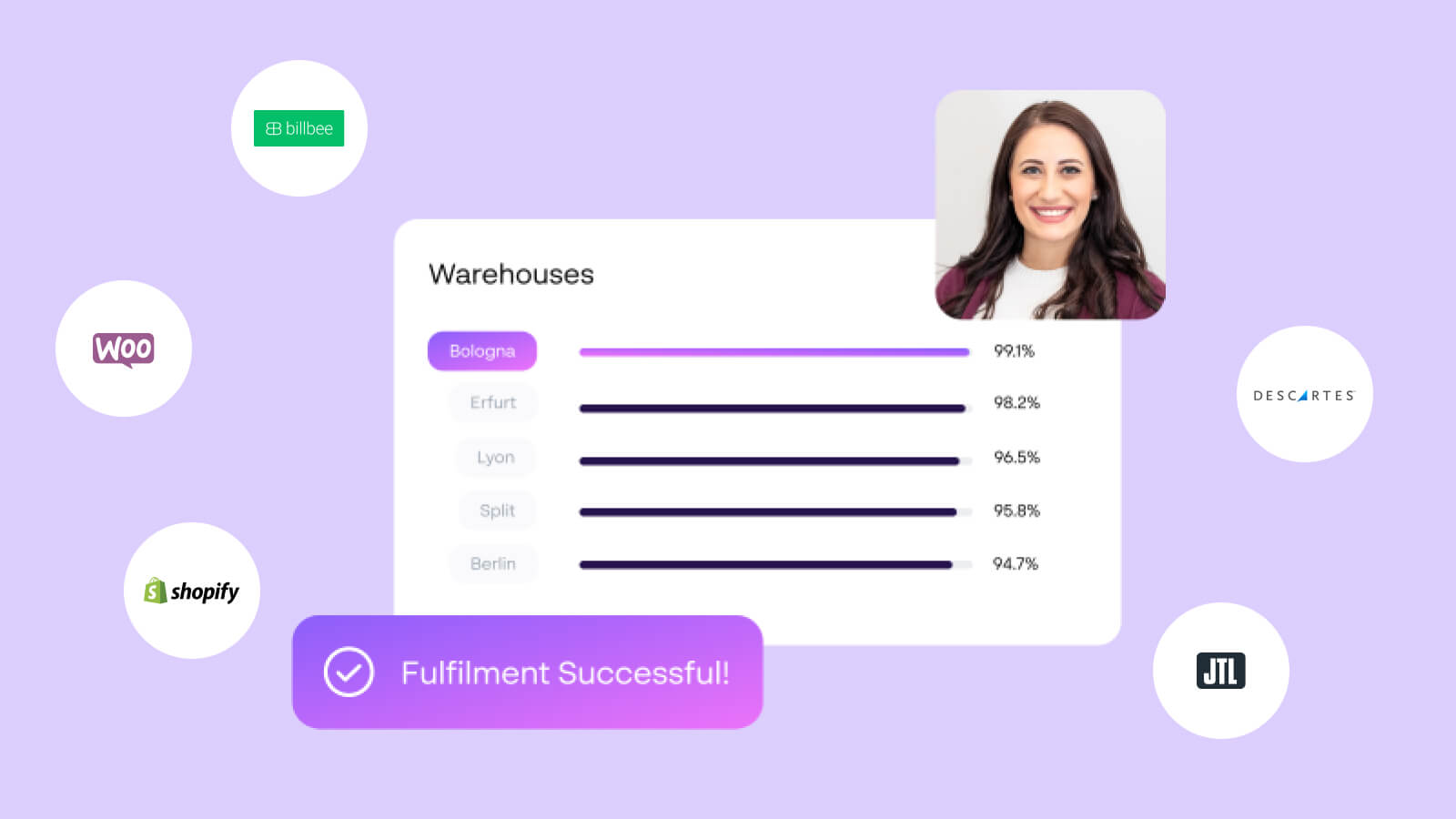
Codept’s one-time integration allows businesses to ‘plug-and-play’ additional partners and integrations as networks expand and connections between multiple ecommerce platforms and 3PLs are required.
Cost
Assessing the total cost of implementation is vital when choosing an automated fulfilment solution. Consider not only the initial investment but also ongoing maintenance costs, software licensing fees and potential training expenses.
Calculate the potential return on investment (ROI) and evaluate the long-term cost savings and operational efficiencies that the solution can provide.
Codept’s one-time connection and intuitive interface streamlines onboarding, saving time and money.
Outsourcing automated fulfilment to a third-party provider
Outsourcing automated fulfilment to a third-party provider can offer numerous benefits - let's explore these aspects in more detail…
- Expertise and Infrastructure: Third-party providers specialising in automated fulfilment have extensive expertise and infrastructure dedicated to efficient order processing and delivery. They possess the necessary technologies, equipment and skilled personnel to handle fulfilment operations effectively.
- Scalability and Flexibility: Outsourcing to a third-party provider allows businesses to leverage the provider's scalable infrastructure and adapt to fluctuating order volumes. This is particularly beneficial for merchants selling seasonal items; if less warehouse space is needed, this is easily adjustable as providers can quickly modify resources and staffing levels to meet peak demands, ensuring timely order fulfilment. Dropshipping is also an effective solution to cope with seasonal demands, since this allows ecommerce merchants to offer products in their online shop without storing or shipping items themselves. This ensures the merchant does not remain stuck with unsold goods. Using Codept’s solution enables dropshipping through fast, secure, and error-free data flow between manufacturers, wholesalers, online merchants and carriers.
- Reduced Capital Expenditure: By outsourcing automated fulfilment, businesses can avoid substantial upfront investments in equipment, software, and infrastructure. Instead, they can benefit from the provider's existing resources and pay for services based on usage or contractual agreements.
- Focus on Core Competencies: Outsourcing fulfilment allows businesses to focus on their core competencies, such as product development, marketing, and customer engagement. By offloading the complexities of fulfilment to a specialised provider, companies can allocate their resources and efforts to strategic areas of growth and differentiation.
- Faster Time-to-Market: Third-party providers with established automated fulfilment capabilities can expedite the implementation process. Businesses can quickly onboard and integrate with the provider's systems, reducing the time required to launch or scale their fulfilment operations. This accelerated time-to-market can be particularly advantageous when businesses need to rapidly respond to market demands or seasonal peaks.
- Risk Mitigation: By entrusting fulfilment operations to a third-party provider, businesses can mitigate risks associated with technology investments, system failures and operational disruptions. Providers are responsible for maintaining and upgrading their systems, ensuring high availability and managing potential risks. This allows businesses to focus on their core operations without the burden of dealing with fulfilment-related risks.
- International Expansion: For businesses looking to expand globally, outsourcing automated fulfilment to a third-party provider with an established international network can be highly advantageous. These providers often have fulfilment centres in multiple countries, enabling faster and more cost-effective international shipping, customs compliance and localised customer support. This is particularly beneficial for merchants shipping hazardous goods due to special law regulations they must comply with.
Selecting the right automated fulfilment solution requires a thorough evaluation of scalability, integration capabilities and cost considerations. Codept’s Tender Management solution helps businesses make an informed decision by identifying the most suitable partners for their assortment needs.
So, is automated fulfilment the future?
The answer lies in striking the right balance between automation and human oversight.
While automated fulfilment offers numerous benefits, it is essential to recognise the importance of human involvement in ensuring quality control and customer satisfaction.
While automation streamlines processes, humans provide the critical element of judgement, problem-solving and adaptability. Human oversight is necessary to monitor automated systems, address exceptions or errors and make decisions when unexpected situations arise.
By combining the efficiency of automation with human expertise and oversight, businesses can create a future of automated fulfilment that optimises operations, maintains quality control and delivers exceptional customer experiences.
FAQs about Automated Fulfilment
How does automated fulfilment enhance order processing efficiency?
Automated fulfilment streamlines the order processing workflow by leveraging technologies such as robotics, conveyor systems and intelligent software. These technologies enable faster and more accurate order picking, packing, and shipping, reducing human errors and optimising operational efficiency.
Will automation replace human workers in the order processing industry?
While automation plays a significant role in order processing, it is important to note that human workers still have crucial roles in overseeing and managing automated systems. Human oversight ensures quality control and exception handling.
What are the benefits of implementing automated fulfilment?
Automated fulfilment offers several benefits, including increased order accuracy, faster order processing and shipping, improved inventory management, reduced operational costs, and enhanced customer satisfaction. It allows businesses to scale their operations efficiently and handle higher order volumes with ease.
How can automated fulfilment adapt to changing customer demands?
Automated fulfilment systems can be flexible and adaptable to changing customer demands. They can handle various order types, including single-item orders, multiple-item orders and customisations.
Additionally, automated systems can be easily reprogrammed or reconfigured to accommodate new products or changes in order processing requirements.
What are the challenges of implementing automated fulfilment?
Implementing automated fulfilment can pose challenges such as the initial capital investment required for technology acquisition and implementation, the need for employee training and change management, potential disruptions during the transition period, and ensuring seamless integration with existing systems.
With proper planning and execution, these challenges can be overcome, and the long-term benefits of automated fulfilment outweigh the initial obstacles. By working with Codept, businesses can rest assured that integrations between shop-, ERP- and WMS-systems and algorithms will work frictionlessly, tested and optimised by our IT experts, making sure your system runs exactly as you need it to.